It’s been a while since Shapeways, and then i.materialize eliminated ceramic materials from their material offerings. No doubt, ceramic wasn’t a big profit center at those companies. The math didn’t pencil out to offer it at prices consumers were willing to pay. The prints were expensive and the designers tasked with selling reproductions on the marketplace were not likely able to; A $90 tea light holder is a big ask to get someone to buy.
But, there is a definite interest in additive ceramic. Smaller players like Tethon 3D and Formlabs have a ceramic resin product, and designers have been able to create some amazing things using it.
Cups Made With Formlabs Ceramic Resin - Photo Formlabs Prints by Tethon - The Roman Singularity City in Ceramics, Photo by Antonio Palmieri
Tethon is entering the hardware market with its Bison 1000, which might be a very neat acquisition for a successful ceramicist who wants to push the boundaries of what the material can do.
For the hobbyist/prosumer, there are some FDM style printers. From the Netherlands we have LUTUM by VormVrij which has been used to produce some very beautiful work. It’s also quite expensive. CERAMBOT out of China actually looks to be getting off the ground and is about to release its entry-level machine to their Kickstarter backers and the general public sometime in Q2 2019. It has some great potential for designers willing to work within its constraints.
Photo - CERAMBOT Origami Sake Set - By Bre & Co. Made with a LUTUM printer.
But, it would help if you had a lot of other resources to make a ceramic product. Ceramic is not something the average apartment dweller will be able to do at home. Besides the printer, you need a place to dry the wet print, a place to glaze it, and a kiln or some method to fire it. For the average hobbyist or designer being able to farm out an idea for a ceramic design to the likes of Shapeways or i.materialise was a convenient (albeit expensive) way to bring those ideas to life in a unique material.
I liked being able to experiment with ceramic 3D prints. It was because of one of those experiments that I came across Kwambio. A customer asked if I could provide her with several copies of a spike cup I had made using Shapeways’ discontinued porcelain material.
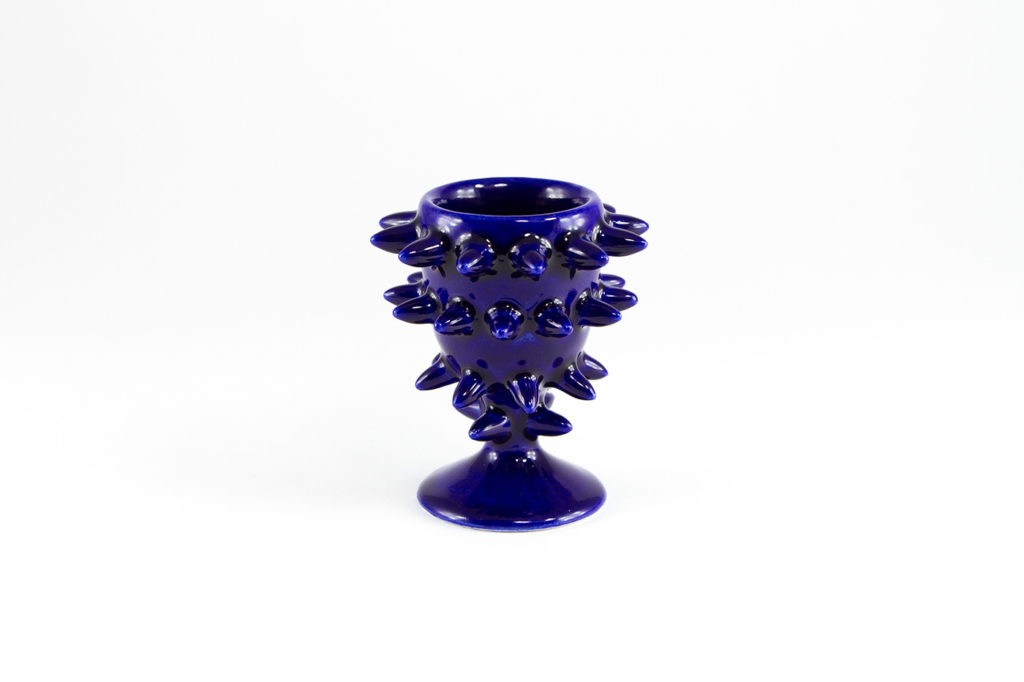
I don’t like telling a customer something can’t be done without at least doing some digging - one of the good things I learned from being an attorney. I explained that no major 3D printing house does ceramic anymore, so I’d have to use a smaller place and see what it would cost and if I would have to make changes to the design.
I went over to Tethon because I knew they did some production in the past, but they seem to have discontinued that service. After some internet sleuthing, I discovered Kwambio. They are a materials/printer startup with production facilities in Ukraine and offices in London and New York. The production facilities are what intrigued me since they offered a wide variety of glazes and colors. I did some more poking around and felt they looked more or less like a legitimate 3D printing enterprise.
I reached out, and Natalia Rybachok soon wrote back. I explained what I needed and asked what they needed from me. They examined the file that I made for the old Shapeways specifications and let me know what needed to be changed for a successful print. Changes were made, and a quote was received. The price was on par with getting the cup made in SLS nylon, so I was on board, and my customer was willing to work with me as well. Natalia was quick and professional despite the time zone lag, and I was impressed with her customer service and patience with walking me through their process.
Spike Cups
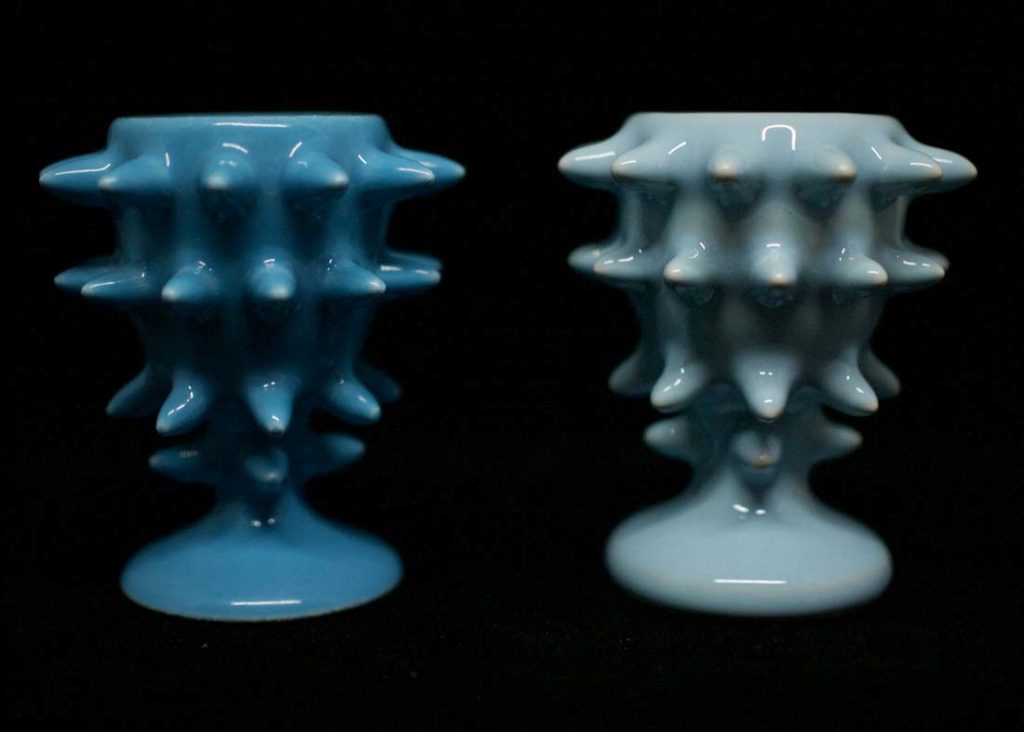
I used my porcelain prints as a baseline for comparison. If Kwambio could approximate that standard at what seemed like a reasonable price, I’d be happy. I ordered some copies in a gloss glaze and color similar to what my customer liked. I also ordered an experimental cup. Then I sat back and waited. The cups themselves were quickly printed, I’d say in under ten days. Shipping was the bottleneck. UPS cost more than I wanted to pay, and the other option was Ukrposhta, which was less expensive but a long wait. I checked with my customer, and time wasn’t an issue for her order, so I opted for the less expensive route.
left: Shapeways Porcelain; right: Kwambio Ceramic left: Shapeways Porcelain; right: Kwambio Ceramic
When the cups made their way through Europe, over the Atlantic, and over to Pittsburgh, I opened the box, and I was impressed. The cups in the blue glaze looked phenomenal. The Kwambio prints didn’t have the high fidelity of the old Shapeways prints - the spikes weren’t as pointy and needed a more gradual fillet where they met the surface of the cup - but they were good enough for what they needed to be.
The difference is design specs stems from the fact that Shapeways did on-demand slip casting - printing molds, pouring the slip, etc. - and was able to create a consistent porcelain copy of a design, though for a price concomitant with all the work involved.
Height Differences
The Kwambio prints are not created that way. Each print is done from scratch. You’ll notice, each blue cup is slightly different in height and stands somewhat different from the others. They probably sagged a bit during the drying process since they needed to support their weight sooner than the Shapeways slip cast pieces had to. A support structure could possibly be sorted for a more extensive run, but for a one-off or just a few-off, this individuality is OK. And let me repeat, I really like the glaze on these cups. They look lickable like polished candy.
One of Kwambio’s extra services that I REALLY liked, which was never offered by the big service bureaus, is the multitude of glaze colors and the ability to specify the placement of those colors on a single print. You can even explore making custom colors and get metallic glazes like silver and gold - would love to see a copper color. I took advantage of this for my experimental cup.
Thorn Cup
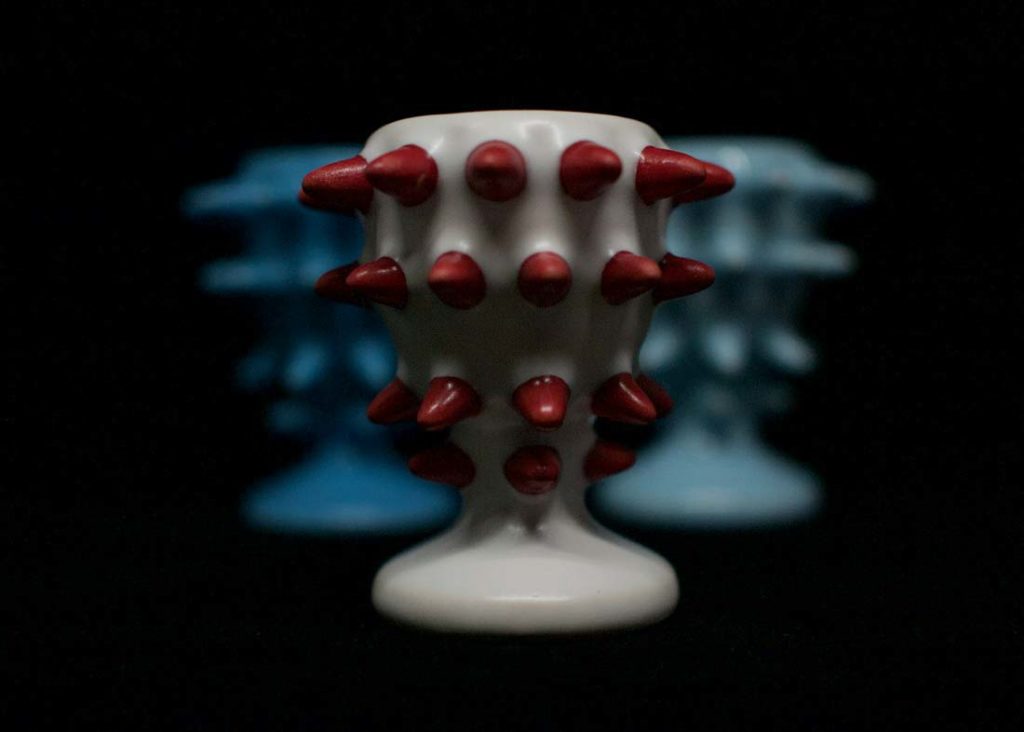
I had Kwambio color each protrusion blood red while leaving the cup white. And I also had them use a matte glaze. This experiment exceeded my expectations. It added an extra bit of interestingness to an older piece, and I think this aspect of their service is ripe for creative use. For an artist or designer that gets comfortable using Kwambio for production of their work, they offer tiered pricing for larger runs of a single design. If they can nail shipping or offer direct to client shipping, then Kwambio’s future looks bright.
I had a great experience using them, and if you want to experiment with ceramic 3D printing and don’t have access to a fully set up studio, they are probably your best bet.
Check out the design guidelines below and tag @joycomplex and @kwambio on Instagram with your ceramic 3D prints. I'd love to see what you come up with.
Kwambio, Inc.
Odessa, Ukraine